Understanding How Ditch Assist Works
- Ditch Assist’s primary function is to sustain a target elevation with the implement blade. This target elevation can be derived from one of the following: a ‘best-fit’ design generated through Slope-IQ, which is based on a survey and operator input; a pre-established land leveling design created in third-party software and loaded into the Ditch Assist app; or a straightforward target grounded on a specified elevation (for instance, when leveling an area to a particular elevation), or on a grade plane depending on a starting elevation.
- The Ditch Assist Control Module obtains GPS location data from the GPS system. This information is then wirelessly transmitted to the Android device that is operating the Ditch Assist App.
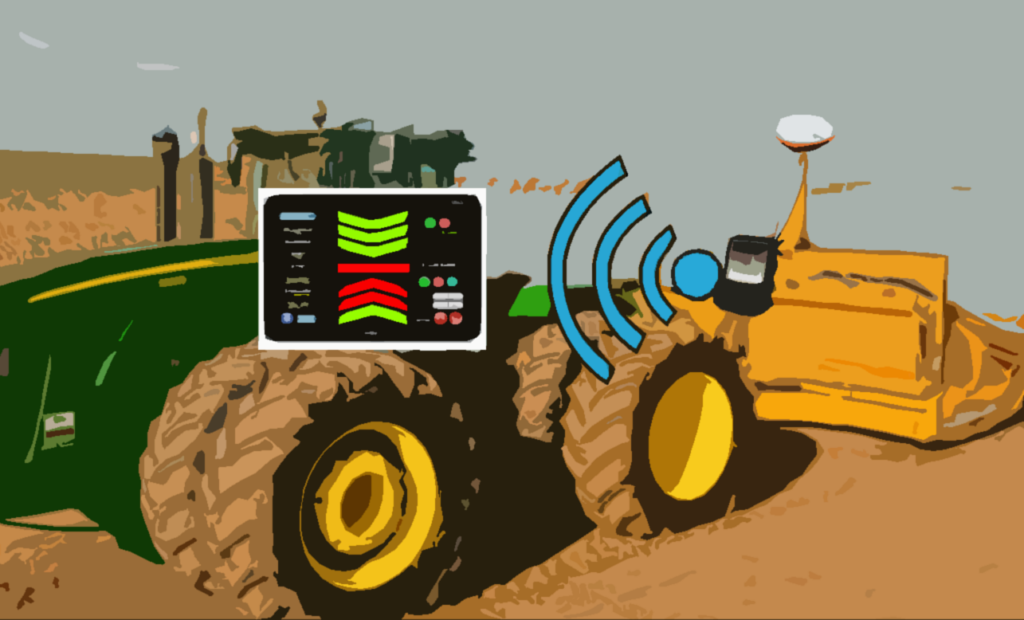
- Based on the current location, the Ditch Assist app determines the target elevation for that point. It then conveys this information to the Control Module.
- The Control Module compares the intended elevation with the actual one, thus establishing the required response – that is, deciding whether the implement needs to be elevated or lowered to achieve the desired level. This adjustment is initiated by activating the solenoids of the PWM valve, leading to vertical movement. Due to the continuous motion of the vehicle and implement, coupled with minor fluctuations even with RTK, precisely attaining the target is almost unachievable. This results in a constant cycle of minute adjustments, fluctuating between raising and lowering, in an effort to reach the target. While subtle movements might go unnoticed, more significant variances will lead to noticeable changes in the hydraulic cylinders’ positions to modify the implement’s height.
Important GNSS (GPS) Limitations to Understand
Ditch Assist heavily relies on precise GNSS (Global Navigation Satellite System) information. A lack of high-accuracy positioning data can result in less than optimal performance.
1. Non-RTK GNSS: Standard GNSS systems like GPS, without the added precision of Real-Time Kinematics (RTK), can have position errors up to several meters. For a system like Ditch Assist, which requires centimeter-level precision, this can lead to inaccuracies in the alignment and leveling of the land. For instance, a non-RTK GNSS might cause the implement to be moved when it’s not necessary, or it might fail to signal when the implement does need to be moved, leading to uneven terrain.
2. Performance Issues with RTK: While RTK provides more precise positioning data than standard GNSS, it isn’t immune to performance issues. RTK requires a stable communication link between the base station and the receiver, and disruptions to this link can result in temporary loss of RTK’s centimeter-level precision. For instance, if the radio link fails or the base station loses its own GNSS signal, the receiver might switch back to standard GNSS accuracy until the issue is resolved. This can result in similar inaccuracies to those experienced with non-RTK GNSS.
3. Multipath Errors: Both non-RTK GNSS and RTK can be affected by multipath errors, which occur when satellite signals are reflected off nearby objects before reaching the receiver. These reflected signals can confuse the receiver, leading to incorrect position calculations. In the context of Ditch Assist, this could mean incorrect implement adjustments.
4. GNSS Signal Blockage: This can be a problem in areas with tall trees, buildings, or other obstacles that might block the line of sight to the GNSS satellites. The loss of signals from some satellites can decrease the accuracy of the position calculations. For Ditch Assist, this could again lead to errors in implement movement.
The use of RTK GNSS technology can mitigate some of these issues, providing higher accuracy for precision agriculture applications like Ditch Assist. However, users should still be aware of potential sources of error and work to minimize them for the best performance.